Edge AI for Predictive Maintenance
Empower your maintenance operations with Edge AI technology for predictive maintenance. Improve equipment reliability and reduce downtime with real-time insights.
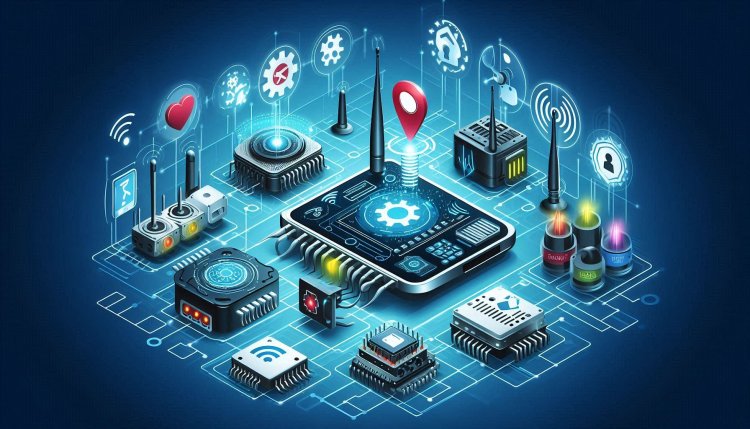
Edge AI for Predictive Maintenance
Predictive maintenance is a proactive maintenance strategy that aims to predict when equipment failure might occur, allowing for maintenance to be performed just in time to prevent downtime and reduce costs. Edge AI, or artificial intelligence at the edge, is revolutionizing the field of predictive maintenance by enabling real-time analysis of data directly on the edge devices, such as sensors and equipment, without the need for constant connectivity to a central server.
Benefits of Edge AI for Predictive Maintenance
There are several key benefits of using Edge AI for predictive maintenance:
- Real-time Analysis: Edge AI allows for real-time analysis of data directly on the edge devices, enabling faster detection of potential issues and quicker response times.
- Reduced Downtime: By predicting equipment failures in advance, maintenance can be scheduled during planned downtime, reducing the impact on production and minimizing unplanned downtime.
- Cost Savings: Predictive maintenance helps to reduce maintenance costs by preventing costly equipment failures and minimizing the need for emergency repairs.
- Improved Safety: By identifying potential issues before they escalate, predictive maintenance helps to improve workplace safety by reducing the risk of accidents caused by equipment failures.
- Extended Equipment Lifespan: By addressing issues before they lead to catastrophic failures, predictive maintenance can help to extend the lifespan of equipment and reduce the frequency of replacements.
How Edge AI Works for Predictive Maintenance
Edge AI for predictive maintenance typically involves the following steps:
- Data Collection: Data is collected from sensors and equipment in real-time, capturing information such as temperature, vibration, and other key indicators of equipment health.
- Data Preprocessing: The collected data is preprocessed on the edge device to clean and format the data for analysis, removing any noise or irrelevant information.
- Model Training: Machine learning models are trained on the preprocessed data to learn patterns and trends that indicate potential equipment failures.
- Model Inference: The trained models are deployed on the edge devices to continuously analyze incoming data and provide real-time predictions of equipment health.
- Alerts and Notifications: When the models detect anomalies or potential failures, alerts and notifications are sent to maintenance teams, enabling them to take proactive action.
Challenges of Implementing Edge AI for Predictive Maintenance
While Edge AI offers numerous benefits for predictive maintenance, there are also some challenges to consider:
- Data Quality: Ensuring the quality and reliability of the data collected from edge devices is crucial for accurate predictive maintenance models.
- Model Optimization: Developing and optimizing machine learning models that can run efficiently on edge devices with limited processing power and memory can be challenging.
- Security Concerns: Protecting sensitive data and ensuring the security of edge devices from cyber threats is essential for successful implementation of Edge AI for predictive maintenance.
- Integration with Existing Systems: Integrating Edge AI solutions with existing maintenance systems and workflows can be complex and require careful planning and coordination.
Case Study: Edge AI for Predictive Maintenance in Manufacturing
One industry where Edge AI for predictive maintenance is making a significant impact is manufacturing. In manufacturing facilities, downtime due to equipment failures can result in substantial losses in terms of production and revenue. By implementing Edge AI for predictive maintenance, manufacturers can proactively monitor the health of their equipment and prevent costly downtime.
For example, a manufacturing plant may deploy sensors on critical machinery to collect data on factors such as temperature, pressure, and vibration. This data is then analyzed in real-time using Edge AI algorithms to detect patterns that indicate potential equipment failures. Maintenance teams can receive alerts and notifications when anomalies are detected, allowing them to schedule maintenance before a breakdown occurs.
What's Your Reaction?
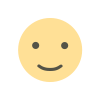
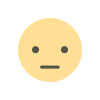
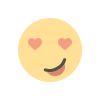
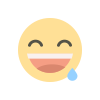

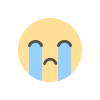
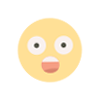