3D Printing: From Prototyping to Production
Explore the evolution of 3D printing from prototyping to production, and learn how this innovative technology is shaping the future of manufacturing.
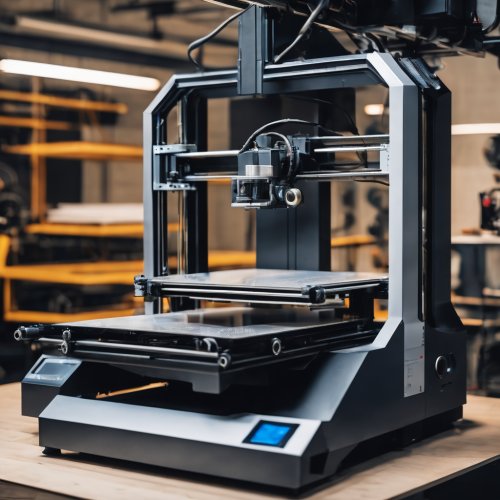
3D Printing: From Prototyping to Production
3D printing, also known as additive manufacturing, has revolutionized the way products are designed, prototyped, and manufactured. Initially used for rapid prototyping, 3D printing technology has advanced significantly and is now being used for production in various industries. From aerospace and automotive to healthcare and consumer goods, 3D printing is transforming the manufacturing landscape.
Prototyping with 3D Printing
One of the key advantages of 3D printing is its ability to quickly and cost-effectively create prototypes. Traditional prototyping methods can be time-consuming and expensive, especially for complex designs. With 3D printing, designers can turn their ideas into physical prototypes in a matter of hours, allowing for faster iteration and refinement of designs.
By using 3D printing for prototyping, companies can reduce the time and cost involved in the product development process. It also allows for more creative freedom in design, as complex geometries and intricate details can be easily produced with 3D printing technology.
Transitioning to Production
While 3D printing was initially limited to prototyping, advancements in materials and technology have made it possible to use 3D printing for production as well. Additive manufacturing offers several benefits for production, including the ability to create complex geometries, reduce material waste, and customize products at scale.
For small batch production or customized products, 3D printing can be a cost-effective and efficient manufacturing solution. Traditional manufacturing methods often require expensive tooling and long lead times, making them impractical for small production runs. 3D printing eliminates the need for tooling and can produce parts on-demand, making it ideal for agile manufacturing.
Applications in Different Industries
3D printing is being used across a wide range of industries for both prototyping and production. In the aerospace industry, 3D printing is used to create lightweight and complex components for aircraft and spacecraft. This not only reduces the weight of the vehicles but also improves fuel efficiency and performance.
In the healthcare sector, 3D printing is revolutionizing the production of medical devices, implants, and prosthetics. Custom implants can be designed and produced quickly, improving patient outcomes and reducing the risk of rejection. 3D printing is also being used to create patient-specific models for surgical planning, allowing surgeons to practice procedures before operating on patients.
The automotive industry is also embracing 3D printing for production. Companies are using additive manufacturing to create custom car parts, tooling, and even entire vehicles. This allows for rapid prototyping and customization, giving companies a competitive edge in the market.
Challenges and Future Outlook
While 3D printing offers numerous benefits, there are still challenges that need to be addressed for widespread adoption in production. These include limitations in material properties, production speed, and post-processing requirements. As technology continues to advance, these challenges are being overcome, paving the way for more widespread adoption of 3D printing in production.
The future of 3D printing looks promising, with ongoing research and development focused on improving materials, processes, and scalability. As the technology becomes more advanced and cost-effective, we can expect to see 3D printing used in even more industries and applications.
Conclusion
3D printing has come a long way from its origins as a prototyping tool to becoming a viable production technology. Its ability to create complex geometries, reduce lead times, and customize products at scale makes it a valuable asset for manufacturers across various industries. As technology continues to evolve, we can expect 3D printing to play an increasingly important role in the future of manufacturing.
What's Your Reaction?
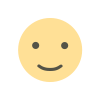
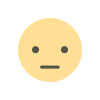
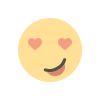
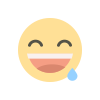

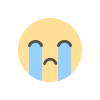
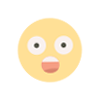