Advances in Wind Turbine Blade Manufacturing
Stay updated on the latest advancements in wind turbine blade manufacturing techniques and technologies. Learn about innovative processes and materials.
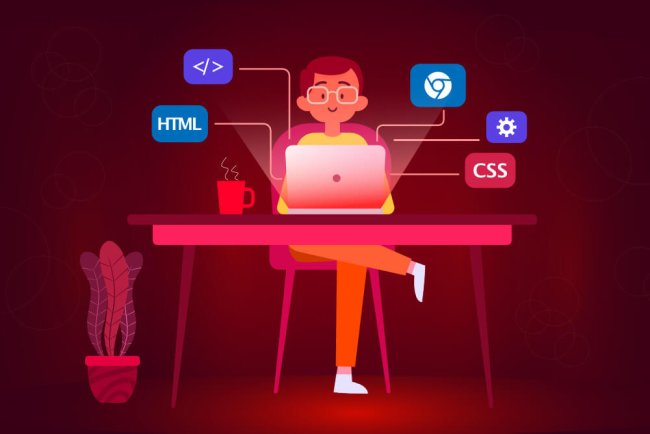
Advances in Wind Turbine Blade Manufacturing
Wind energy is a rapidly growing sector in the renewable energy industry, and wind turbine blades play a crucial role in harnessing this clean and sustainable energy source. Over the years, there have been significant advances in the manufacturing of wind turbine blades to improve their efficiency, durability, and cost-effectiveness. Here are some key developments in wind turbine blade manufacturing:
1. Materials
One of the most important aspects of wind turbine blade manufacturing is the choice of materials. Traditionally, fiberglass has been the primary material used for constructing wind turbine blades due to its lightweight and durable properties. However, there has been a shift towards using carbon fiber composites and other advanced materials to create longer and lighter blades that can capture more wind energy. These materials offer higher strength-to-weight ratios, allowing for larger blades that can withstand higher loads and generate more electricity.
2. Manufacturing Processes
Advancements in manufacturing processes have enabled the production of more precise and efficient wind turbine blades. Automated manufacturing techniques such as robotic layup and 3D printing have revolutionized blade production, allowing for greater consistency and quality control. These processes help reduce manufacturing time and costs while improving the overall performance of the blades.
3. Design Optimization
Design optimization plays a crucial role in maximizing the energy output of wind turbine blades. Advanced computer-aided design (CAD) software and simulation tools allow engineers to create blade designs that are tailored to specific wind conditions and site requirements. By optimizing the aerodynamics and structural integrity of the blades, manufacturers can improve efficiency and reliability while reducing maintenance costs over the lifespan of the turbine.
4. Integration of Sensors
The integration of sensors into wind turbine blades has become more prevalent in recent years. These sensors can monitor various parameters such as blade deflection, temperature, and structural loads in real-time, allowing for early detection of potential issues and proactive maintenance. By collecting and analyzing data from these sensors, operators can optimize the performance and lifespan of the blades, leading to increased energy production and reduced downtime.
5. Modular Blade Designs
Modular blade designs have gained popularity in the wind energy industry as they offer greater flexibility and scalability. By dividing the blade into smaller sections that can be easily transported and assembled on-site, manufacturers can reduce transportation costs and logistical challenges associated with large blade sizes. Additionally, modular designs allow for easier maintenance and repair, minimizing downtime and improving overall turbine availability.
6. Sustainability
Sustainability has become a key focus in wind turbine blade manufacturing, with manufacturers striving to reduce the environmental impact of blade production and disposal. Recycling initiatives for end-of-life blades, such as repurposing materials for other applications or converting them into new composite materials, are being explored to minimize waste and promote a circular economy. Additionally, efforts are being made to optimize manufacturing processes to reduce energy consumption and emissions throughout the lifecycle of the blades.
7. Testing and Certification
Rigorous testing and certification processes are essential to ensure the safety and reliability of wind turbine blades. Advancements in testing technologies, such as digital twin simulations and full-scale blade testing facilities, have improved the accuracy and efficiency of blade certification. By subjecting blades to various mechanical and environmental tests, manufacturers can verify their performance under different operating conditions and ensure compliance with industry standards and regulations.
8. Industry Collaboration
Collaboration between stakeholders in the wind energy industry, including manufacturers, researchers, and government agencies, has been instrumental in driving innovation in wind turbine blade manufacturing. By sharing knowledge and resources, industry partners can collectively address challenges and explore new opportunities for improving blade design, manufacturing processes, and performance. This collaborative approach fosters a culture of continuous improvement and accelerates the development of cutting-edge technologies in the field.
Conclusion
Advances in wind turbine blade manufacturing have significantly enhanced the efficiency, reliability, and sustainability of wind energy systems. By leveraging new materials, manufacturing processes, design techniques, and sensor technologies, manufacturers can produce high-performance blades that maximize energy production and minimize environmental impact. Continued research and collaboration within the industry will drive further innovation and help propel the growth of wind energy as a clean and viable source of power for the future.
What's Your Reaction?
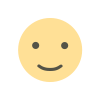
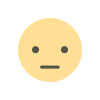
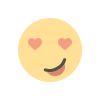
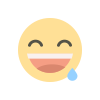

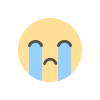
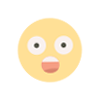